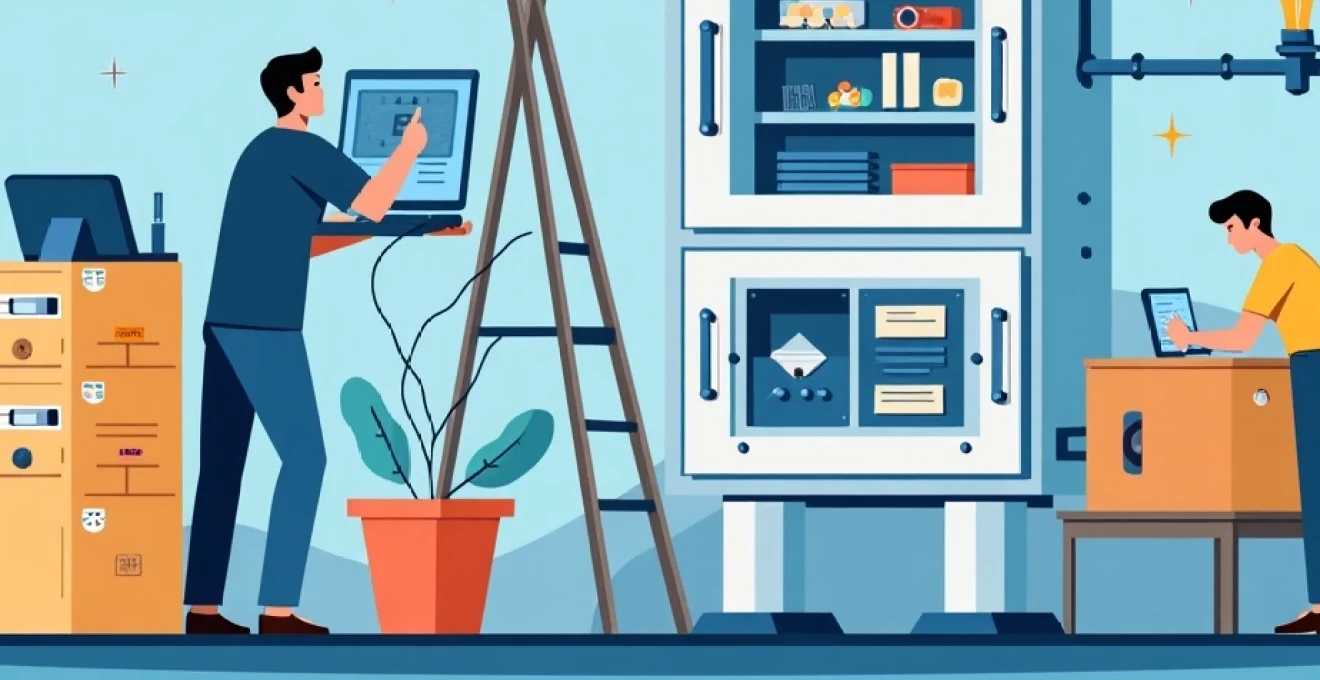
In today's technologically driven world, electrical equipment forms the backbone of countless industries and businesses. From manufacturing plants to office spaces, the smooth operation of electrical systems is crucial for productivity and safety. Regular maintenance of electrical equipment is not just a recommendation; it's a necessity that can significantly impact efficiency, safety, and the longevity of your assets. By implementing a robust maintenance program, you can prevent unexpected downtime, reduce the risk of electrical accidents, and optimize the performance of your equipment.
Electrical maintenance encompasses a wide range of activities, including inspections, testing, cleaning, and repairs. These tasks, when performed consistently and correctly, can identify potential issues before they escalate into major problems. This proactive approach not only saves money in the long run but also ensures a safer working environment for your employees. Let's delve into the key aspects of electrical maintenance and explore how you can establish an effective routine to keep your systems running smoothly.
Establishing a regular maintenance schedule
The foundation of effective electrical maintenance lies in creating and adhering to a well-structured schedule. A systematic approach ensures that no equipment is overlooked and that all maintenance tasks are performed at appropriate intervals. When developing your maintenance schedule, consider the specific needs of your facility and the various types of electrical equipment you operate.
Determine frequency based on equipment usage
Not all electrical equipment requires the same level of attention. The frequency of maintenance should be determined based on several factors, including the equipment's age, usage patterns, and manufacturer recommendations. For instance, heavily used machinery in a production line may need more frequent checks compared to office equipment that sees less intensive use.
To establish an appropriate maintenance frequency:
- Review manufacturer guidelines for each piece of equipment
- Consider the operational environment (e.g., exposure to dust, moisture, or extreme temperatures)
- Analyze historical data on equipment performance and failure rates
- Consult with experienced maintenance personnel or electrical contractors
By tailoring your maintenance schedule to the specific needs of each piece of equipment, you can optimize your resources and ensure that critical systems receive the attention they require.
Create a checklist of maintenance tasks
A comprehensive checklist serves as a roadmap for your maintenance activities, ensuring that no critical tasks are overlooked. Your checklist should cover all aspects of electrical maintenance, from basic visual inspections to more complex testing procedures. Here's a sample of items that might appear on your maintenance checklist:
- Visual inspection of wiring, connections, and insulation
- Testing of circuit breakers and fuses
- Measurement of voltage, current, and resistance
- Thermal imaging to detect hot spots
- Lubrication of moving parts in motorized equipment
Remember to update your checklist regularly to incorporate new equipment or changes in maintenance best practices. A well-designed checklist not only ensures thoroughness but also provides a clear record of completed tasks for compliance and auditing purposes.
Assign responsibilities to qualified personnel
Electrical maintenance is not a task to be taken lightly. It requires specialized knowledge and skills to perform safely and effectively. When assigning maintenance responsibilities, ensure that your team members have the appropriate qualifications and training. This might include:
Certified electricians for complex repairs and installations
Trained maintenance technicians for routine inspections and basic troubleshooting
Safety officers to oversee compliance with electrical safety regulations
Investing in ongoing training for your maintenance team can pay dividends in terms of improved efficiency and reduced risk of accidents. Consider partnering with professional electrical safety training programsto keep your team's skills up-to-date.
Visual inspection of electrical components
Visual inspections form the first line of defense in your electrical maintenance strategy. Regular visual checks can help identify many potential issues before they develop into serious problems. These inspections should be conducted systematically, covering all accessible parts of your electrical system.
Check for signs of wear or damage
During visual inspections, look for any obvious signs of wear, damage, or deterioration. This includes:
- Frayed or exposed wires
- Corroded connections or terminals
- Cracked or discolored insulation
- Signs of overheating, such as melted plastic or burn marks
- Loose or missing fasteners
Pay particular attention to areas subjected to mechanical stress, extreme temperatures, or environmental factors like moisture or dust. Early detection of these issues can prevent more serious problems and potential safety hazards.
Ensure proper connections and wiring integrity
Proper connections are crucial for the safe and efficient operation of electrical systems. During your visual inspection, verify that all connections are tight and secure. Look for:
- Loose wire connections at terminals
- Signs of arcing or sparking
- Proper wire routing and support
- Correct wire gauge for the application
Remember, even a single loose connection can lead to overheating, energy loss, or equipment failure. If you spot any issues, address them promptly or schedule a follow-up with a qualified electrician.
Verify functioning of indicators and displays
Many electrical components feature indicators or displays that provide valuable information about their status and operation. During your visual inspection, ensure that these elements are functioning correctly:
- Check that all indicator lights are working
- Verify that digital displays are clear and readable
- Confirm that analog meters are moving freely and providing accurate readings
Malfunctioning indicators can mask underlying issues, so it's essential to address any discrepancies promptly. If you're unsure about the readings or behavior of any indicators, consult the equipment manual or seek advice from a specialist.
Testing and calibration procedures
While visual inspections are important, they can't reveal all potential issues within an electrical system. Regular testing and calibration procedures are essential to ensure that your equipment is operating within specified parameters and to detect any hidden problems.
Start by establishing a comprehensive testing protocol that covers all critical aspects of your electrical system. This should include:
- Insulation resistance testing to check for deterioration in wire insulation
- Ground resistance testing to ensure proper grounding
- Load testing to verify that equipment can handle its rated capacity
- Power quality analysis to identify issues like harmonics or voltage fluctuations
- Thermal imaging to detect hot spots that may indicate potential failures
When conducting these tests, it's crucial to use calibrated test equipment to ensure accurate results. Regularly calibrate your testing instruments according to manufacturer recommendations and industry standards. This not only ensures the reliability of your test results but also helps maintain compliance with safety regulations.
For complex testing procedures or specialized equipment, consider engaging professional electrical testing services. These experts have access to advanced diagnostic tools and can provide detailed reports on the condition of your electrical systems.
Accurate testing and calibration are the keys to identifying potential issues before they become critical problems. Don't underestimate the importance of these procedures in your maintenance routine.
Cleaning electrical equipment and surroundings
Maintaining a clean environment for your electrical equipment is crucial for its longevity and efficient operation. Dust, debris, and other contaminants can interfere with proper functioning and even create safety hazards. Implementing a regular cleaning routine as part of your maintenance program can significantly reduce these risks.
Remove dust debris from components
Dust accumulation on electrical components can lead to overheating and reduced efficiency. To properly clean your equipment:
- Use compressed air to blow out dust from hard-to-reach areas
- Wipe down external surfaces with anti-static cloths
- Vacuum larger debris, ensuring the vacuum is rated for use around electrical equipment
- Pay special attention to cooling fins and ventilation openings
Always ensure that equipment is powered down and locked out before beginning any cleaning procedures. This precaution is essential for both safety and to prevent accidental damage to sensitive components.
Clean air filters and ventilation systems
Proper airflow is critical for the cooling of electrical equipment. Regularly cleaning air filters and ventilation systems helps maintain optimal operating temperatures and prevents overheating. Follow these steps:
- Inspect air filters monthly and replace as needed
- Clean ventilation grilles and fan blades to remove dust buildup
- Ensure that air intake and exhaust paths are unobstructed
- Consider using high-efficiency filters in dusty environments
By maintaining clean air filters and ventilation systems, you can significantly extend the life of your electrical equipment and reduce energy consumption.
Ensure proper clearance around equipment
Adequate clearance around electrical equipment is not just a matter of accessibility; it's a critical safety requirement. Proper clearance helps prevent overheating and reduces the risk of fire. To maintain proper clearance:
- Remove any stored items or debris from around electrical panels and equipment
- Ensure that all required warning signs and labels are visible and unobstructed
- Maintain clear access paths to all electrical equipment for easy maintenance and emergency access
- Verify that clearance meets or exceeds local electrical code requirements
Regularly inspect the areas around your electrical equipment to ensure that proper clearance is maintained. This simple practice can prevent many potential hazards and improve the overall safety of your facility.
Documenting maintenance activities and findings
Thorough documentation is a crucial aspect of any effective electrical maintenance program. Proper record-keeping not only helps track the history of your equipment but also aids in identifying recurring issues, planning future maintenance, and demonstrating compliance with safety regulations.
To create a comprehensive documentation system:
- Develop standardized forms for recording maintenance activities and inspection results
- Use digital tools or software to organize and store maintenance records
- Include detailed descriptions of any issues found and actions taken
- Attach photos or thermal images to illustrate specific problems
- Record dates of maintenance activities and schedule future tasks
Consistent and detailed documentation can provide valuable insights into the performance and reliability of your electrical systems over time. This information can be invaluable when making decisions about equipment upgrades or replacements.
Consider implementing a computerized maintenance management system (CMMS)to streamline your documentation process. These systems can help automate scheduling, track inventory, and generate reports, making it easier to manage your maintenance program effectively.
Well-maintained documentation is not just about record-keeping; it's about building a knowledge base that can inform better decision-making and improve the overall effectiveness of your maintenance strategy.
Regular maintenance of electrical equipment is an investment in the safety, efficiency, and longevity of your systems. By establishing a comprehensive maintenance program that includes scheduled inspections, testing, cleaning, and documentation, you can significantly reduce the risk of electrical failures and associated hazards. Remember that electrical maintenance should always be performed by qualified personnel, and when in doubt, don't hesitate to seek the expertise of professional electrical contractors.